Category Archive: DFT® Valves
Natural Gas Service for Power Plants
As economic growth rises, so does the demand for natural gas. The infrastructure for natural gas in power plants should keep up with the unique challenges posed by power production and distribution. For instance, the need for gas compression and metering facilities in the Utica and Marcellus Shale regions has increased dramatically in the last few years. Experts predict that this area will provide about 43% of all U.S. natural gas supplies by 2025, so the infrastructure to support this increase should also advance.
Natural gas is a cleaner, more efficient alternative to traditional energy sources in power generation boiler systems, compressor lines, and other applications. Power plant outages are most common in April and May of every year, so power generation professionals should also update their systems to address these concerns.
Learn more about the challenges power plants face and the solutions that can alleviate them.
Industry Challenges for Power Plants
As power production evolves, the industry grapples with the complexities of distributing energy globally through patchwork power grids and adapting to thermal cycling for on-demand energy production. Thermal cycling is an efficient yet demanding process that subjects conventional power plant components to excess stress, causing rapid wear, noise, and vibration. The rigorous start-stop cycles not only risk premature failures but also compromise the durability of essential parts.
The differentiation between simple cycle and combined cycle gas plants also introduces additional complexities in component selection, as each type of plant presents distinct operational demands. This scenario highlights an urgent need for parts, particularly valves, that are robust enough to endure the harsh conditions of power generation.
Natural Gas Service Solutions
In the demanding area of power generation, the critical need for specialized valve products has never been more pressing. These valves serve as the cornerstone of system integrity, ensuring precise and controlled flow in pumps, boilers, and compressors. Check valves, in particular, prevent reverse flow and reduce system surges.
Applications facing high pressures and temperatures, such as steam and water lines or boiler feeds, necessitate the use of silent check valves and severe service control valves. These specialized valves are meticulously designed to withstand the demanding conditions found in these and other applications, like cooling towers, evaporators, and vacuum systems. They’re essential in preserving the continuous and reliable function of these critical power generation components, thereby safeguarding the infrastructure’s operational integrity and efficiency.
DFT® Excalibur Check Valves
DFT® Excalibur check valves are specifically engineered to address the unique demands of non-reciprocating compressor service and pump applications within the power generation sector. Incorporating innovative spring-assist technology, DFT® Excalibur check valves prevent reverse flow, thereby reducing the risks of water hammer and vibration—common issues that can compromise system integrity and equipment lifespan.
The engineering behind Excalibur valves not only provides reliability and ease of maintenance but also delivers an extended service life. Its durability and performance equate to considerable long-term cost savings for the facility.
Available in a range of line sizes from 2″ to 24″ and ASME Class 150 to 1500, Excalibur valves offer versatility to meet the varied needs of power generation applications. Other features include:
- ASME B16.10 Face-to-Face Dimensions
- Standard body materials: A216 Grade WCB Carbon Steel, A351 CF8M Stainless Steel
(and other options available) - RF flanged standard ends
- Optional ends: butt weld, flanged x butt weld, RTJ, Victaulic®
- Center-guided and dual-guided stem
- Two-piece body
- Vertical or horizontal installation
- Spring-assisted, silent closing non-slam
- API 6FA (consult DFT factory for applicable sizes and classes)
DFT® can custom size to your specific application, enhancing overall system efficiency and safety.
DFT® Excalibur Check Valves for Natural Gas Service Applications
Over eight decades, DFT® has established a legacy of excellence in valve manufacturing, earning the trust of the power generation industry. Our Excalibur valves showcase our commitment to innovation, quality, and the safety of both personnel and equipment within power plants. As the energy sector navigates the growing demand for natural gas services and confronts the evolving challenges of power production, DFT® leads the industry in providing premium in-line check valves and severe service control valves.
Learn more by reading a case study about the success of our valves in a power plant well pump application. To get started on your natural gas service solution, request a quote or contact us today.
Severe Service Check Valves
DFT® manufactures check valves for many applications, including severe service applications. Typically, when engineers think of severe service, they think of high temperatures and/or high pressures. However, severe service applications also include high cycling applications. We are going to explore two high cycling applications, including the challenges and DFT®’s severe service valve solutions.
Digester Service
The paper pulp digester is the primary equipment used in the production of chemical pulp. It is used to cook raw materials for papermaking (e.g., wood, grass, bamboo, and others) to produce pulp mainly containing cellulose by chemical interaction with the cooking liquor.
This process includes steam injection at up to 150 PSIG. The steam is pulsed into the digester several times per hour. While 150 PSIG is not considered severe, the constant pulsing can take a toll on equipment.
Digester Solutions
Several end users have experienced premature failure of traditional swing-type check valves in this application. When the swing check valves fail, the black liquor used to break down the pulp and the pulp itself would migrate upstream past the failed swing check and damage upstream piping and equipment.
The end users reached out to DFT® to develop an Axial Flow Non-Slam Check Valve solution to this problem. DFT® developed several styles of severe service check valves with special construction to handle this high cycling application. The DFT® solutions include the GLC® SS short-pattern flanged check valve, the Excalibur® SS a B16.10 long-pattern flanged check valve, and the WLC® SS wafer-style check valve.
All of these check valve styles have upgraded internal materials selected to withstand constant high cycling. The upgraded materials include 17-4 trim with a Xylan-coated one-piece welded disc stem assembly, 17-4 bushings, and an X-750 spring.
Compared to only getting several months of service life with the swing check valves, end users now get extended years of service life with the DFT® Axial Flow Non-Slam Digester Severe Service Valve solution.
Boiler Feedwater Service
All power plants—including natural gas-fired, coal-fired, and nuclear power plants—have boilers. The boilers generate steam to power turbines that generate electricity. Water must be heated in boilers to generate steam. The water is delivered to the boilers by boiler feedwater pumps.
Boiler feedwater is typically in the range of 180 °F to 225 °F. These temperatures would not be considered severe. However, depending on the design of the system in power plants, the temperature may be even higher, often 300°F to 350°F , especially if feed water is preheated by economizers or heaters using steam from the turbine or other heat recovery processes. Feedwater pump discharge pressures can vary between 700 and 1400 psi depending on boiler demand.
Check valves are installed between the outlet of the boiler feedwater pumps and the inlet of the boilers and/or deaerators. The check valves are installed to prevent backflow out of the boiler that can damage expensive feedwater pumps and other upstream equipment. Not only is this a high-cycling operation, but it is also a high-pressure application with varying pressures depending on boiler load. This is a very demanding application. As with the digester application, traditional swing checks typically experience a high failure rate in this application.
Boiler Feedwater Solutions
DFT® developed the WLC® BF specifically for boiler feedwater applications. The WLC® BF has upgraded hardened materials selected to withstand high pressure, pressure swings, and high cycling. The upgraded materials include a WL9 body, a 4 ribbed body construction, greater wall thickness, 410 trim, a one-piece welded disc stem assembly with Colmonoy-coated stem, carburized bushings, and an X-750 spring.
Compared to only getting several months of service life with the swing check valves, end users now get extended years of service life with the DFT® Axial Flow Non-Slam Boiler Feedwater Severe Service Valve solution.
Valve Types
DFT® offers the following valve types for digester, boiler feedwater, and other severe service applications. These valves are constructed from high-quality, heavy-duty materials with tight seals to withstand the harsh operating conditions of their application:
- DFT® Model WLC® BF (Boiler Feed): The DFT® Model WLC® BF wafer style check valve is for severe duty boiler feed service applications and other severe duty applications.
- DFT® Model GLC® SS: The DFT® Model GLC® SS is a severe service short-patterned flanged silent check valve designed for digester applications and other severe service applications.
- DFT® Model WLC® SS: The DFT® Model WLC® SS is a severe service wafer style check valve for digester applications and other severe service applications.
- DFT® Excalibur SS: The DFT® Excalibur SS is a severe service flanged silent check valve for digester applications and other severe service applications. This valve is B16.10 and a direct replacement for a swing check valve.
Severe Service Check Valves by DFT® Inc.
Severe service applications require specialized valve solutions. DFT® Inc. offers an extensive product line of robust severe service silent check valves specifically designed for these high-pressure and high-temperature environments. We are certified by ISO 9001:2015 and many other valve standards such as 3-A Sanitary Standards, Manufacturers Standardization Society (MSS), American Petroleum Institute (API) SPEC 6D, and European Pressure Equipment Directive (PED) to provide quality, long-lasting valves you can depend on.
Request a quote for your severe service valve solution today.
Vacuum Breakers in the Textile Industry
To facilitate this production, manufacturers increasingly turn to specialized machinery that can meet the demands of consumer, military, and industrial standards. Regardless of the machine or textile itself, however, most of these machines require the same underlying equipment: boiler and compressor systems that use vacuum breakers, chemical lines, and condensate lines.
Applications of Vacuum Breakers in the Textile Industry
A vacuum breaker is a specialized valve that protects pressure vessels, as well as pressurized tanks and piping. The textile industry has uses for vacuum breaker check valves and control valves throughout numerous stages of production. Some of the most common applications of these components include:
- Regulating heat from steam boilers. This heat has uses in fabric dyeing and drying processes.
- Creating pressure relief points. Valves allow pressure release for air compressor systems that need to run continually without downtime.
- Controlling the flow rate and volume of fluids. Accomplished along with the help of metering pumps, valves ensure a steady, sufficient flow of liquids such as chemicals and water. They also discharge substances from boilers, compressors, and pumps.
Vacuum Breaker Benefits in the Textile Industry
Vacuum breakers help create safer systems, with some of the tasks they can handle including:
- Stopping pipe collapses if the transient pressure drops
- Breaking siphons
- Stopping water hammer by allowing more air into the downstream portion of the piping after the check valve
- Preventing the formation of dangerous vacuums
Why You Need Vacuum Breakers
Vacuum breakers can protect your pressurized system from impairment in the event of pressure loss or over pressurized systems. They prevent dry can, slasher collapse, and pressure vessel collapse. In steam heated drying cylinders, which often dry ink on printed fabric, internal steam can condense into water during system downtime, creating a vacuum in the cylinder. Guarding against this, vacuum breakers can help keep your textile systems running efficiently and on time.
Vacuum breakers provide a tight shutoff to stop steam from leakage when a system is in use and then allow steam to escape during cooling cycles. Without vacuum breakers, the pressure shifts between highly pressurized “on” periods and depressurizing “off” periods can jeopardize the integrity of your equipment and lead to costly damage and downtime.
Vacuum Breakers From DFT® Inc.
The right vacuum breakers have strong seals to prevent leakage but are responsive enough to allow for the release of steam as needed to keep your textile operations running smoothly across each stage of production. Whether your facility specializes in synthetic fabrics, organic and natural fabrics, or dyed and treated textiles, the right equipment makes all the difference in completing orders on schedule and creating consistent products.
At DFT®, we serve our customers with a wide range of check valves and control valves. Our durable stainless steel DFT® Vacuum Breakers (model BSSV) are available in 1-inch to 4-inch diameters with a lapped disc and seat for tight shutoff. Contact us today or download our flyer to learn more about our Vacuum Breakers. You can also request a quote if you are ready to start your order.
Reverse Osmosis and Purified Water
Clean water is important for industrial processes, but the water a facility receives may not be clean enough. Using a reverse osmosis (RO) purification system can provide the level of purity companies need for product specifications and quality standards. Reverse osmosis water purification is a common technique for removing impurities from water for use in processing everything from pharmaceuticals to food and beverages. Systems using reverse osmosis rely on durable check valves to dependably manage reverse flow and water hammer to purify contaminated water.
Why Check Valves for the Reverse Osmosis Industry?
Different check valves provide different benefits, functionalities, and levels of control at various stages. For example, a check valve located after water exits the membrane housing stops backflow and ensures that permeate water continues out the outlet port. Check valves are also required components for reverse osmosis systems that have automatic shut-off valves and pressurized tanks. When a tank is full, it creates enough back-pressure that it could send water surging backward through the system, causing breakage or recontamination. A spring-assisted valve can stop purified water from exiting back through the membrane. Flow only begins again after the back-pressure is below the feed pressure.
While check valves can protect the reverse osmosis setup, they do experience harsh conditions. Corrosive seawater and chemical contaminants can degrade these valves. Over time, dissolved salts (ions), chloride, and other chemicals will break down the seal and housing, which can lead to contaminated water. However, facilities can reduce the risk of deterioration by choosing the right seals and housings for the expected contaminants and environmental conditions. Nickel-aluminum-bronze and duplex stainless steel valves, for example, can withstand constant exposure to seawater. These materials are commonly used in check valves for reverse osmosis/desalination plants throughout Saudi Arabia, Israel, and the coast of California.
Reverse Osmosis Applications and Industries
Water purity is especially essential for the production of consumable goods, and reverse osmosis systems used along with other water treatment systems meet this challenge. Two of the most common industries with applications for reverse osmosis valves are:
- Food and beverage. Reverse osmosis can purify water to guarantee safety, consistency, quality, and controllable tastes and odors in the final products.
- Pharmaceuticals. Pharmaceutical manufacturers cannot create safe products without pure water. Even trace amounts of bacteria, organic material, chemicals, or minerals can jeopardize a product. In fact, some of the strictest water purity mandates call for water that has 10,000 times lower impurity levels than safely rated drinking water.
No matter the industry or water source, DFT® Inc. manufactures and distributes check valves that can keep reverse osmosis equipment running smoothly. Four of our highly recommended RO valves are:
- GLC® NAB (Nickel-Aluminum-Bronze) Silent Check Valves
- GLC® (Duplex Stainless Steel) Silent Check Valves
- Excalibur® NAB (Nickel-Aluminum-Bronze) Silent Check Valves
- Excalibur® (Duplex Stainless Steel) Silent Check Valves
These check valves have a spring-assisted and non-slam design with applications in pressurized systems for preventing water hammer and in systems with exposure to extremely harsh conditions. With their use in brine, brackish water, and more, check valves are rated to withstand corrosion and deter marine life. They also feature a nozzle style for easy operation and require little maintenance.
Choose Reverse Osmosis Check Valves From DFT®
Reverse osmosis systems can purify water to make it safe for drinking, industrial processes, and pharmaceutical and food production. In those systems, check valves allow for safe and efficient water processing. For over 75 years, DFT® has innovated to provide its customers with in-line check valves and severe service control valves to fit their specific needs. Contact us today to learn more about our capabilities, or request a quote to start your order.
DSV® Sanitary Check Valves in the Pharmaceutical Industry: Explore Our eBook
In sanitary manufacturing applications that employ the use of fluid systems, such as in the pharmaceutical industry, regulating fluid flow and pressure is essential to maintaining high product and production quality. Common issues—such as backflow, water hammer, and cleanliness – significantly affect the overall effectiveness and efficiency of the system. For these situations, DSV® sanitary check valves serve as an ideal solution.
Why Are DSV® Sanitary Check Valves Important?
Unlike other check valves available on the market, DSV® sanitary valves meet 3A sanitary standard and are designed for use in applications with high sanitation requirements. As such, they are ideal for the manufacturing operations of products intended for consumption or direct contact with consumers, where unsanitary conditions can result in illness or injury. 316L stainless steel offers the corrosion resistance needed to prevent the contamination of process fluids.
By eliminating crevices and cavities from the valve design and achieving smooth, polished finishes on internal and external surfaces, we minimize the risk of material and bacteria buildup in our valves. We test 100% of our check valves before shipping them out to customers.
Get Your Free Copy:
A Guide to DSV® Sanitary Check Valves in the Pharmaceutical Industry
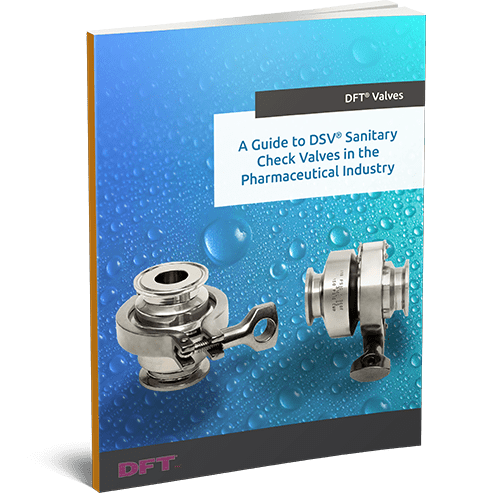
Download Now
Additional Information on DSV® Valves
Construction
The valve consists of seven main components: body, seat, disc, spring, guide, clamp, and body gasket. Both the disc and seat are lapped to ensure tight shutoff capabilities.
For full valve construction, check out our eBook.
Types
- Horizontal Valves. The horizontal valve models are suitable for use in horizontal piping lines that require a self-draining valve.
- Vertical Valves. The vertical valve models are designed for use in vertical piping lines or horizontal piping lines that do not require a self-draining valve.
Key Features
- Meets 3A Standard 58-02
- 32 Ra or 15 Ra finish
- Clean-in-Place Design
- And more…
Download Now: All key features found in our eBook!
Applications
- Condensate lines
- Evaporators
- Vacuum breakers
- Purified Water
- And more…
Download Now: All applications listed in our eBook!
A DFT® DSV® Sanitary Check Valve Success
A major engineering firm contacted us on behalf of several pharmaceutical companies. The firm needed to find a check valve solution for their noncorrosive medical waste drain system. The check valve needed to operate at 20 psig or less with a flow of 3 GPM, have sanitary end connections, provide tight shutoff, have a low cracking pressure to open and be able to be steam cleaned in place.
The check valve had to withstand high temperatures, as the firm used 330°F steam to clean the entire medical waste process system 3 times a day. The valve also needed an extremely smooth finish to maintain sanitary conditions.
Responding to the challenge, a DFT® 2 inch DSV® vertical check valve was specified. Designed to prevent flow reversal, this non-slam, full-body valve came equipped with a 0.1-psi cracking pressure spring. We also designed it with tri-clamp connections for ease of disassembly. The product was so successful that… Get the full story in our eBook!
For additional information about our DSV® valves and how they suit the needs of the pharmaceutical industry, download our eBook today.