Category Archive: DFT® Valves
Valve Tips for Fall Shutdowns
Fall shutdown season is upon us.
Once a year, generally in September, manufacturers spanning every industrial sector — from metal stampers to power plants — shut down for anywhere between 1 to 3 weeks. As you well know, these fall shutdowns are not company-wide vacations; instead, they allow facilities to perform the important cleaning, repairs, maintenance, component or system replacements, and facility inspections required to keep your plant running smoothly at peak efficiency for another year.
In preparation for your fall shutdown, you should be working with a valve manufacturer to ensure that all of your valves are functioning properly or, when they are not, to repair or replace them. Fall shutdown is the ideal time to do so.
Common Valve Repair Problems
Valves are an important aspect of many industrial processes but there are perhaps no facilities more dependent on their proper functioning than power plants. Manufacturing facilities and power plants alike tend to run across three problems when attempting to repair their valves.
Many facilities, particularly older ones that have not had a full overhaul in a number of years, have older valves. Plant and maintenance managers often prefer to repair these valves rather than replace them. Often, however, they will find that the original valve manufacturer is no longer in business and that the required valve repair kits are no longer available.
The second common problem is that, even when they are repairable, a facility’s valves may be so old that they have become obsolete. Valve technology and manufacturing is constantly improving — there is a high chance that your old valves introduce a potentially costly inefficiency that, though unavoidable at the time of installation, has been corrected by newer valve technology.
Finally, many plant and maintenance managers find that the cost of repairing older valves and fitting them with replacement parts can be prohibitively expensive. This can be particularly true in facilities that deal of condensate, such as power plants.
DFT® Inc. and Fall Shutdowns
With more than 70 years of valve manufacturing experience, DFT® Inc. is a leading control and check valve manufacturer.
Prior to shutdowns, DFT can work with your planners and maintenance team to provide education on the new valve technologies available for your facility. DFT is available to evaluate your valves and your piping system as a whole, to help reduce turbulence and potential failure. Our team can help guide you through the process. Our experts will help you to determine whether cleaning and repair is a viable option, or if you should consider replacing your valves with newer valve technologies.
If you determine that replacement is the better option for you, we will provide those replacements for you within the timeframe of your shutdown. Typically we replace failing swing and double door check valves with a newer technology provided by spring assisted, silent check valves.
Learn More
From the world renowned DFT® Silent Check Valves to the innovative DFT® HI-100™ Control Valves, DFT®’s team of valve experts has experience providing recommendations to a variety of industries. Industries served include power generation, petroleum production & refining, building maintenance, chemical processing, water treatment, food & beverage, and more.
Facilities with steam applications, namely power plants, often experience high levels of condensation which, when not managed properly can cause any number of problems — rust and scale, lubrication degradation, reduced performance, and even machinery failure, to name a few.
We strongly encourage our power plant clients to consider the SCV® valve 3” and smaller for condensate and steam applications. Learn more about the SCV® valve by downloading the spec sheet.
Our larger diameter flanged and wafer style valves are available in sizes through 36” and larger pressure classes ranging from 125#-2500#.
Maintenance & Replacement Valves Blog Series:
Vacuum Breakers and Their Applications
Valves play an integral part in many applications performed by anyone from a manufacturer to an engineer to a construction manager. The basic function of a valve is to control both the flow and pressure within a process or system. The functions of a valve include:
- Regulating a flow or process pressure
- Relieving a system of pressure
- Stopping or starting a flow
- Increasing or reducing a flow
- Controlling the flow’s direction
Keeping this in mind, a Vacuum Breaker Check Valve provides effective protection against collapse of pressure vessels, tanks and piping. This particular valve prevents condensate “back-up” when equipment is shut down or inlet steam is reduced by modulating control valves. Within a piping system, DFT® Vacuum Breakers can perform helpful tasks, such as:
- Breaking a siphon
- Preventing pipe collapse during transient pressure drops
- Providing additional air on downstream side of check valves to help prevent water hammer
This variation of a check valve, or Vacuum Breaker, features a spring-assisted silent closure. If there is no pressure on the valve, the spring pushes the disc into a closed position. Other features include:
- 1” to 4” size range (MNPT)
- 450 to 6000 CWP
- Threaded O.D. with unthreaded inlet bore
- Stainless steel construction
- Horizontal or vertical installation
- Tight shutoff – lapped disc and seat
- Inconel X-750 Spring
- soft seat options
The wide variety of DFT® Vacuum Breakers makes it easy to find and install the one that’s correct for any application. Beyond their use in building water systems, they can be used in anything from chemical processing to power generation to pharmaceutical applications.
With so many applications requiring a strict no-backflow function, we’ve compiled a list of codes and standards, as well as industry applications into a downloadable catalog. Select the button below to download our free eBook, Vacuum Breaker Check Valves: Your Defense Against Pipe Collapse & Pressure Vessel Damage.
DFT® Expansion Features Added Warehouse Space and State-of-the-art Training Facility
Good things are happening at DFT! We have just completed a 10,800 square foot expansion to our Headquarters located in Exton, Pennsylvania. The expansion includes additional warehouse space to support new machinery, inventory equipment, and an on-site training facility.
The facility expansion consists of major inventory enhancements, which includes a Vertical Storage Retrieval System (VSRS), an automated system to facilitate the storage, protection, and retrieval of stock. The VSRS stands 18 feet high and its innovative vertical design allows for 1,224 square feet of storage space, while taking up only 155 square feet of floor space.
Additional machinery includes two vertical Doosan turning centers, which will enable more in-house production with decreased turnaround time. Two five-ton overhead crane systems will assist in maneuvering products throughout the warehouse and expedite order fill rate.
The new state-of-the-art training facilities will enable DFT to host large groups for check valve and control valve product training. These training sessions are held twice a year and are open to both distributors and end users. Customers can enroll in one of these hands-on training sessions by contacting a DFT® Regional Sales Manager.
DFT’s warehouse expansion is an exciting step in our continuous journey to improve your customer experience. The added capacity for manufacturing, inventory, and training will help us to improve production and supply chain capabilities, as well customer service and satisfaction.
Click on the following link to view DFT’s full press release featured on leading industry news platforms PRWeb and ThomasNet.
Choose a Rewarding Career with DFT, Inc.
Finding an ideal career is vital for your personal and professional growth. Once you’ve started down a career path, you need to find a company that can encourage this growth—you deserve nothing less.
At DFT, Inc., we are a tight-knit company that is highly dedicated to our employees and customers alike. DFT has been a leading manufacturer of fully customized, world class check valves and control valves for over 70 years.
Since the beginning, we have always listened to the needs of our customers; our first product, the Basic-Check® valve, was specially designed to provide tight shut-off while in any position. As the years progressed, the application requirements of our customers grew, and as such, our capabilities grew as well. The technical proficiency of the DFT team led to the innovation of unique valve products, capable of delivering high performance to any industrial application.
Open Positions
Today, DFT is a leader in the valve manufacturing industry. DFT’s success is attributed to our commitment to providing the highest level of customer satisfaction; this commitment begins with selecting talented individuals to join our company. Our newly launched Career Page currently has the following open positions:
- CNC Machinist
Our machinists organize and operate computer numerical control (CNC) machines to create the metallic components of our valve products. This position revolves around meticulous attention to detail regarding blueprints, drawings, and other documents to determine part tolerances and dimensions and set up requirements.CNC machinists are also responsible for the smooth operation of machinery, and they must verify that all created workpieces meet DFT’s quality expectations.
- Valve Assembly
In this position, you will be assembling seats, discs, stems, and other prepared machine parts into a diverse array of valves. Responsibilities include lifting and securing workpieces, part inspection and testing, and elimination of scratches and other imperfections through lapping, grinding, or polishing.Additionally, valve assemblers will work toward maintaining safe and clean working environments.
DFT, Inc. has grown into a global leader in the valve industry. We are proud of our accomplishments, but we never rest on our laurels; we can always improve and grow as a company, and we seek employees that are like-minded.
If you’re interesting in joining DFT, please contact us for more information.
DFT’s Arie Bregman and Jeff Kane Receive VMA Awards
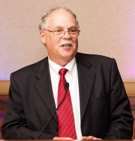
DFT’s Arie Bregman is VMA’s Person of the Year
Management, technical, and engineering professionals gathered in Tucson, Arizona for the Valve Manufacturers Association of America (VMA) annual meeting. The meeting took place this past September, and it gave VMA members the opportunity to host conferences, programs, and exhibits pertaining to the valve and actuator industry.
This is the largest U.S. gathering of industry professionals, and it gives them the opportunity to discuss critical issues and current trends. The event also presents the chance to interact with consumers and market analysts; it is also the Association’s platform to recognize industry professionals who have made outstanding contributions. (more…)