Category Archive: Uncategorized
Benefits of Vacuum Breaker Check Valves
What It Is
Vacuum breaker check valves relieve unwanted low-pressure conditions within closed systems. They are installed directly into the system and allow air to enter the system when internal pressure drops below atmospheric pressure. When closed tanks are drained of liquid or during a phase change — when water transitions from steam to condensate, for example — the pressure within a pipeline or vessel can fall below atmospheric pressure. This results in a dangerous condition where pressure outside the vessel is greater than pressure inside. A vacuum breaker allows air to enter the system to equalize the pressure and ensure safe operational conditions. Without this safety component, there is the potential for damage, collapse, or rapid implosion. A vacuum breaker can also prevent a siphon and backflow contamination.
How It Works
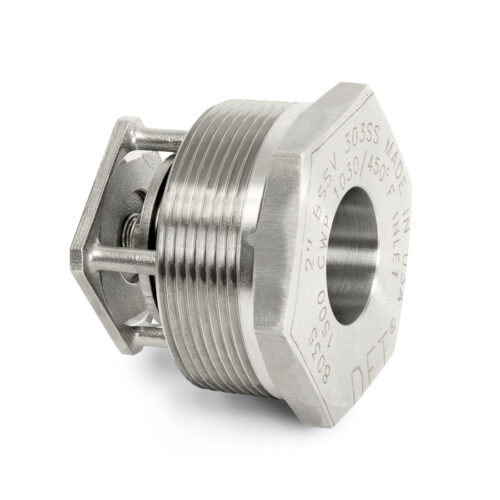
A vacuum breaker check valve is a device that allows for the flow of air in one direction, but closes to prevent flow in the opposite direction. When the system is at normal pressure, the greater pressure inside the system compared to the pressure of the external environment keeps the door of the vacuum breaker shut. A spring assists in keeping the valve closed. When pressure in the system drops below that of the external environment, the valve opens to allow air into the system, equalizing pressure inside and out. The valve spring is selected to control at what pressure difference the valve first opens. The valve spring is designed to allow the valve to open at a set pressure difference (called the “cracking pressure). Valve size selection is important for allowing sufficient airflow into the system, depending on how quickly liquid is being evacuated that needs to be replaced by air or how rapidly pressure is dropping because phase change is occurring. Vessel collapse is prevented.
Once the pressure difference is lowered to an acceptable level, the valve closes, forming a tight seal to prevent outward flow. No system fluid can escape into the atmosphere.
Applications
In addition to preventing damage and even collapse in systems that experience vacuum conditions, vacuum breaker check valves can be used to prevent siphoning of tank discharge lines with terminations below the tank fluid level. These devices can also be used to prevent backflow of liquid into system lines when a discharge pipe terminates under the surface of the liquid in another container. The latter example is commonly seen on outdoor faucets.
Benefits of Vacuum Breaker Check Valves
Vacuum breaker check valves are simple mechanisms that respond quickly to small pressure differences. Their quick action can minimize the risk of vessel or piping collapse. These valves can also keep a fluid system safe by preventing siphon-powered backflow and contamination.
Vacuum Breaker Check Valves From DFT® Inc
DFT® Inc specializes in providing high-quality check valves and control valves to our customers. We build each of our DFT® NPT-threaded Vacuum Breakers (BSSV) from stainless steel, with a lapped disc and seat that provides a reliable seal. These valves are available in sizes ranging from one inch to four inches in diameter. Other sizes, materials, and mating configurations are also available. Contact us today to learn more about our products or request a quote to get started.
Sanitary Check Valves for the Food & Beverage Industry
With end products that must be safe for consumption, the food and beverage industry relies on high-performance parts in its manufacturing processes to prevent bacteria contamination and to meet stringent FDA and USDA regulations. Additionally, systems within this industry must moderate the temperature and humidity of a product for safe processing and spoilage prevention. Sanitary check valves are well suited to the piping systems of the food and beverage sector due to their high-quality stainless steel and polished surface, tight seal, clean-in-place (CIP) ability, reliability, and longevity.
Sanitary Check Valve Features
-
Smooth internal features. Sanitary check valves are made from 316L stainless steel that has a highly polished internal surface that won’t allow buildup to develop. There are no rough surfaces or internal edges where buildup or impurities can cling and begin to degrade the metal or break off into passing fluid. The internal design of sanitary check valves also won’t have any crevices where potential contaminants can become trapped and cause unsanitary conditions. - Tight seal. For sanitary applications in food and beverage processing, the elimination of potential backflow needs to be absolute, and an extremely tight seal addresses this hygienic concern.
- Reliable construction. Sanitary check valves need to be able to last without frequent replacements, degradation over time, or failure. The material composition and design of these valves should ensure low maintenance with a long lifetime.
When you’re looking for the right sanitary check valves, also look for products that meet the material, pressure, and performance standards for your system to comply with governmental and industry regulations.
Benefits of Tri-Clamp Piping Systems
Tri-clamp fittings are a type of leakproof sanitary fitting component that can join endpoints together by clamping a gasket in between two flanged ends. These versatile fittings use external sealing capabilities to make installation, maintenance, and inspections easy, allowing for an array of vertical or horizontal system design configurations. Operators can quickly and easily disassemble the system and valve for cleaning, and this feature is paramount for industrial sectors like food and beverage.
DSV® Valves for the Food & Beverage Industry From DFT® Inc.
For over 75 years, DFT® has served industrial sectors with reliable, quality check valves to ensure efficient, safer operations. We maintain a full line of our DSV® Sanitary Check Valves, which we design, customize, and manufacture to help simplify maintenance and maintain compliance to production and sanitation standards for your organization. We build our sanitary check valves to meet 3-A quality standards and CIP criteria. We specialize in serving the food and beverage markets with food-grade valves for reliable processing applications to prevent reverse flow or bacteria buildup from contaminating products and equipment.
Read our eBook about the critical role of our DSV® Sanitary Check Valves in the food and beverage industry. You can also contact our team to find the right check valves for your facility or request a quote to start your order.
Vacuum Breakers in the Textile Industry
To facilitate this production, manufacturers increasingly turn to specialized machinery that can meet the demands of consumer, military, and industrial standards. Regardless of the machine or textile itself, however, most of these machines require the same underlying equipment: boiler and compressor systems that use vacuum breakers, chemical lines, and condensate lines.
Applications of Vacuum Breakers in the Textile Industry
A vacuum breaker is a specialized valve that protects pressure vessels, as well as pressurized tanks and piping. The textile industry has uses for vacuum breaker check valves and control valves throughout numerous stages of production. Some of the most common applications of these components include:
- Regulating heat from steam boilers. This heat has uses in fabric dyeing and drying processes.
- Creating pressure relief points. Valves allow pressure release for air compressor systems that need to run continually without downtime.
- Controlling the flow rate and volume of fluids. Accomplished along with the help of metering pumps, valves ensure a steady, sufficient flow of liquids such as chemicals and water. They also discharge substances from boilers, compressors, and pumps.
Vacuum Breaker Benefits in the Textile Industry
Vacuum breakers help create safer systems, with some of the tasks they can handle including:
- Stopping pipe collapses if the transient pressure drops
- Breaking siphons
- Stopping water hammer by allowing more air into the downstream portion of the piping after the check valve
- Preventing the formation of dangerous vacuums
Why You Need Vacuum Breakers
Vacuum breakers can protect your pressurized system from impairment in the event of pressure loss or over pressurized systems. They prevent dry can, slasher collapse, and pressure vessel collapse. In steam heated drying cylinders, which often dry ink on printed fabric, internal steam can condense into water during system downtime, creating a vacuum in the cylinder. Guarding against this, vacuum breakers can help keep your textile systems running efficiently and on time.
Vacuum breakers provide a tight shutoff to stop steam from leakage when a system is in use and then allow steam to escape during cooling cycles. Without vacuum breakers, the pressure shifts between highly pressurized “on” periods and depressurizing “off” periods can jeopardize the integrity of your equipment and lead to costly damage and downtime.
Vacuum Breakers From DFT® Inc.
The right vacuum breakers have strong seals to prevent leakage but are responsive enough to allow for the release of steam as needed to keep your textile operations running smoothly across each stage of production. Whether your facility specializes in synthetic fabrics, organic and natural fabrics, or dyed and treated textiles, the right equipment makes all the difference in completing orders on schedule and creating consistent products.
At DFT®, we serve our customers with a wide range of check valves and control valves. Our durable stainless steel DFT® Vacuum Breakers (model BSSV) are available in 1-inch to 4-inch diameters with a lapped disc and seat for tight shutoff. Contact us today or download our flyer to learn more about our Vacuum Breakers. You can also request a quote if you are ready to start your order.
Reverse Osmosis and Purified Water
Clean water is important for industrial processes, but the water a facility receives may not be clean enough. Using a reverse osmosis (RO) purification system can provide the level of purity companies need for product specifications and quality standards. Reverse osmosis water purification is a common technique for removing impurities from water for use in processing everything from pharmaceuticals to food and beverages. Systems using reverse osmosis rely on durable check valves to dependably manage reverse flow and water hammer to purify contaminated water.
Why Check Valves for the Reverse Osmosis Industry?
Different check valves provide different benefits, functionalities, and levels of control at various stages. For example, a check valve located after water exits the membrane housing stops backflow and ensures that permeate water continues out the outlet port. Check valves are also required components for reverse osmosis systems that have automatic shut-off valves and pressurized tanks. When a tank is full, it creates enough back-pressure that it could send water surging backward through the system, causing breakage or recontamination. A spring-assisted valve can stop purified water from exiting back through the membrane. Flow only begins again after the back-pressure is below the feed pressure.
While check valves can protect the reverse osmosis setup, they do experience harsh conditions. Corrosive seawater and chemical contaminants can degrade these valves. Over time, dissolved salts (ions), chloride, and other chemicals will break down the seal and housing, which can lead to contaminated water. However, facilities can reduce the risk of deterioration by choosing the right seals and housings for the expected contaminants and environmental conditions. Nickel-aluminum-bronze and duplex stainless steel valves, for example, can withstand constant exposure to seawater. These materials are commonly used in check valves for reverse osmosis/desalination plants throughout Saudi Arabia, Israel, and the coast of California.
Reverse Osmosis Applications and Industries
Water purity is especially essential for the production of consumable goods, and reverse osmosis systems used along with other water treatment systems meet this challenge. Two of the most common industries with applications for reverse osmosis valves are:
- Food and beverage. Reverse osmosis can purify water to guarantee safety, consistency, quality, and controllable tastes and odors in the final products.
- Pharmaceuticals. Pharmaceutical manufacturers cannot create safe products without pure water. Even trace amounts of bacteria, organic material, chemicals, or minerals can jeopardize a product. In fact, some of the strictest water purity mandates call for water that has 10,000 times lower impurity levels than safely rated drinking water.
No matter the industry or water source, DFT® Inc. manufactures and distributes check valves that can keep reverse osmosis equipment running smoothly. Four of our highly recommended RO valves are:
- GLC® NAB (Nickel-Aluminum-Bronze) Silent Check Valves
- GLC® (Duplex Stainless Steel) Silent Check Valves
- Excalibur® NAB (Nickel-Aluminum-Bronze) Silent Check Valves
- Excalibur® (Duplex Stainless Steel) Silent Check Valves
These check valves have a spring-assisted and non-slam design with applications in pressurized systems for preventing water hammer and in systems with exposure to extremely harsh conditions. With their use in brine, brackish water, and more, check valves are rated to withstand corrosion and deter marine life. They also feature a nozzle style for easy operation and require little maintenance.
Choose Reverse Osmosis Check Valves From DFT®
Reverse osmosis systems can purify water to make it safe for drinking, industrial processes, and pharmaceutical and food production. In those systems, check valves allow for safe and efficient water processing. For over 75 years, DFT® has innovated to provide its customers with in-line check valves and severe service control valves to fit their specific needs. Contact us today to learn more about our capabilities, or request a quote to start your order.
Check Valves in the Natural Gas Industry: Explore Our eBook
Natural gas demand rises in tandem with economic growth. For example, in the Utica and Marcellus Shale areas, the need for metering facilities and gas compression stations has expanded rapidly in recent years. Forecasts suggest that this ongoing infrastructure expansion should continue for the foreseeable future.
Six of the 6” 900# WCB/SS DFT® model PDC® Check Valves were the right solution to replace the piston check valves originally installed for this application.
DFT® Model PDC® Features:
2” to 26” line size- ASME class 150 to 1500
- RF & RTJ flanged ends
- ASME B16.10 face-to- face dimensions
- Standard Body Materials:
- A216 WCB carbon steel
- A351 CF8M stainless steel
- A352 LCC low-carbon
steel
- Stainless steel trim
- Center-guided/dual-guided stem
- Spring assisted silent closing, non-slam
- Tight shutoff – lapped disc & seat
- Horizontal or vertical installation
- Protected spring
- Axial Flow
- Nozzle style
Access our eBook to Learn More about the Role of Natural Gas in Today’s World
Proper check valves reduce the likelihood of malfunctions and potentially catastrophic side effects in your natural gas system. Our new eBook, Check Valves in the Natural Gas Industry, explores:
- Which Check Valves Are Suitable for Natural Gas Applications?
- How long Do DFT® Check Valves Last?
- Construction of the PDC® and GLC® Check Valves
Additional Resources
You can also download our free webinar, Engineered Check Valve Solutions For Natural Gas Applications to learn more about the important role of check valves and how to resolve flow issues and avoid failures.
The experts at DFT® can help you select the best check valves for your needs. If at any time you have additional questions, please contact us or request a quote.