Webinar Q&A: Hydrogen Production and the Role of Engineered Check Valves
As a follow-up to our November 2022 webinar, Hydrogen Production and the Role of Engineered Check Valves, we’re sharing the questions we received from the audience. The answers are provided by host Stephen O’Neill, Director of Sales and Marketing of DFT ® Inc. O’Neill, MBA, is a degreed Mechanical Engineer with 30 years of experience in the valve industry including check valves, control valves, pressure relief valves and pulse jet valves.
In our webinar, Stephen broke down what to know about hydrogen production, including what hydrogen is, how it’s produced, the different methods of storage and more. He also provided in-depth information on the right check valves to use for various hydrogen applications.
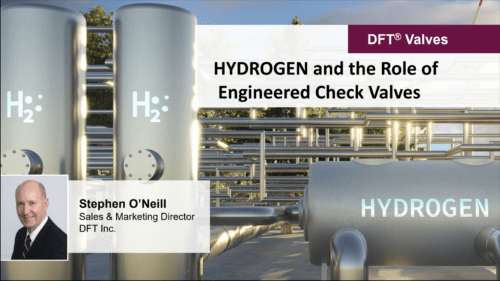
Hydrogen and the Role of Engineered Check Valves Webinar
If you missed the webinar, you can now view it on demand. Simply click this link.
Below, our knowledgeable host answers questions regarding engineered check valves to help you find the right type and fit for your hydrogen application.
Q: Are there any pipelines in the USA (or in the world) with hydrogen injection? If so, what is the percentage of hydrogen? Is any pipeline operator nearing the 15% hydrogen composition?
A: Hydrogen can be injected in Natural Gas pipelines, but only up to 15% of the mix. This can be done, but it is still in the pilot stages.
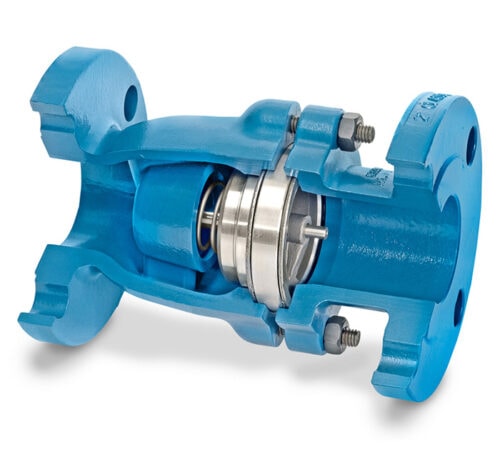
Excalibur® Silent Check Valve
Q: Can the Excalibur be used in temp around 113F to -50F?
A: Yes, the Excalibur can be used in temperatures ranging from 133F to -50F, but in order to function at -50F the valve must be made of stainless steel.
Q: Is there something specific of API6D that only applies to check valves & not generally also to ball valves?
A: This specification defines the requirements for the design, manufacturing, assembly, testing, and documentation of ball, check, gate, and plug valves for application in pipeline and piping systems for the petroleum and natural gas industries.
This specification is not applicable to subsea pipeline valves, as they are covered by a separate specification, API 6DSS.
This specification is applicable to valves for the following pressure ratings only: Class 150, Class 300, Class 400, Class 600, Class 900, Class 1500, and Class 2500.
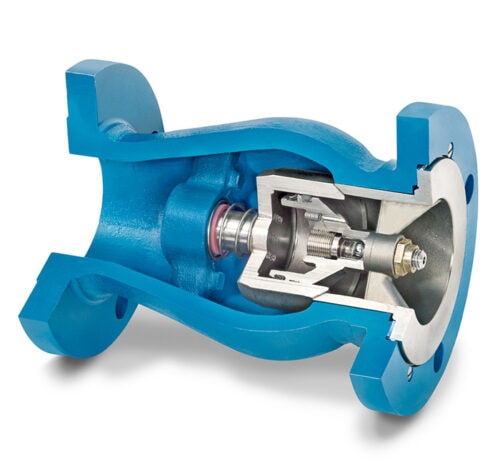
PDC® Silent Check Valve
Q: How many cycles per minute can the PDC valve handle?
A: The PDC does not cycle on and close when it is installed downstream from a reciprocating compressor. The PDC has a built-in pulse dampening chamber that is designed to remain in the open position even as the compressor cycles. The valve does not begin to close until the upstream pressure decreases and begins to approach the cracking pressure.
Q: Would the PDC valve be used in addition or in lieu of the check valves used in a diaphragm compressor?
A: A diaphragm compressor is a variant of the classic reciprocating compressor with backup and piston rings and rod seal. The compression of gas occurs by means of a flexible membrane, instead of an intake element. The back and forth moving membrane is driven by a rod and a crankshaft mechanism. These compressors have built in check valves as part of their assemblies. The PDC would not typically be used in this application.
Q: What is the “special cleaning” required with cryogenic check valves?
A: Special cleaning is required to clean cryogenic valves and piping. This cleaning process is designed to remove oils, grease, and fibers, which may interfere with your system’s functionality or present a flammability hazard depending on the service. After washing the valve’s component parts in a solvent cleaner, workers must inspect them for any residues the cleaning procedures may have missed. In most cases, the valves and pipes should not contain any assembly grease or oils, although there are some approved lubricants for oxygen service components that will not harm the system with their presence. Some customer specs may not allow for the presence of any lint or fibers within the valve. Even if some fiber is allowed, no system should contain fibers greater than 1/8” (3 mm) in length. In oxygen systems, the presence of lint can be quite problematic due to the risk of flammability. It is critical to thoroughly inspect all the components that go into the system to make sure they are free of any and all contaminants. Black light testing allows inspectors to easily identify lint, fibers, or other residue that needs to be removed.
Q: Do you do check valves where the downstream pressure could be intermittently as low as or close to vacuum? Is there some special feature you use for this type of application?
A: DFT makes special check valves for use in vacuum applications. These valves are called Vacuum Breaker Check Valves. These valves have cracking pressures that range from .6 to .15 PSI.
Q: What is the suggested type of check valve for low pressures? (20-40 bar, non-cryogenic)
A: DFT does not consider 20 to 40 bar as low pressure applications. DFT has a side variety of check valves that can handle these pressures. The choice of valve would depend on size, end connection and material requirements.
Q: If liquid hydrogen is needed to be compressed to at least 5,000 PSI, how is the PDC suitable at Class 1,500?
A: 5,000 PSIG exceeds the pressure of a 1500 Class valve. A 2500 Class (non-catalogue) valve would have to be used at these pressures.
Q: Is there a plan to manufacture valves less than 2″ size especially for high pressure hydrogen (>300 barg).
A: We do not offer a PDC in sizes lower than 2 inch, due to restrictions associated with internal components
Q: For Saltwater pump discharge applications, is 316SS internal material available?
A: Yes, 316 internals are available. However, DFT also offers valves made of Nickel Aluminum Bronze material for saltwater applications. NAB may be a better choice.
Q: Do your check valves open only due to flow increase or delta P, or both?
A: DFT check valves are designed to open upon increased upstream pressure and/or decreased downstream pressure. Either condition can result in the .5 cracking pressure. Cracking pressure refers to the inlet pressure level at which the first sign of flow is present. It can also be described as a measure of the pressure differential between the inlet and outlet ports of the valve when flow is initially detected.
Q: Is H2 already used for running vehicles?
A: Yes, but the number is very limited. Hydrogen fueled vehicles require Hydrogen fueling stations. Most of the Hydrogen fueling stations in the US are in California. However, more are planned in other states including Texas. However, there are more than 20,000 forklift trucks that operate on hydrogen fuel cells in the US.
Q: For the reciprocating application, I think you mentioned a spring designed for 1,000,000 cycles. Does that spring cycle with every compressor piston stroke? If so, 1,000,000 cycles is not very long.
A: The PDC does not cycle on and close when it is installed downstream from a reciprocating compressor. The PDC has a built-in pulse dampening chamber that is designed to remain in the open position even as the compressor cycles. The valve does not begin to close until the upstream pressure decreases and begins to approach the cracking pressure.
Q: How do you minimize the back pressure that can be created by the check-valve on upstream equipment?
A: The way to minimize the potential for upstream backpressure is to install springs with low cracking pressure. A spring with a .5 PSIG cracking pressure would result in the release of any upstream backpressure that exceeded the .5 PSIG cracking pressure.
Q: Understanding that the PDC check valve is made for gas, what are the impact of particulates within the gas on the function of the valve (sensitivity to solids carried through)?
A: Particulate interfering with the operation of a PDC pulse dampening check valve is not something that we typically experience. However, if particulate is present in the flow stream and it is present is sufficient volume, it would have the potential to affect the operation of the pulse dampening chamber within the PDC. Scrubbers or separators would typically be installed in gas flow streams to remove such partials before they reach compressors or check valves.
Q: Is cracking a pressure and pressure loss related?
A: Cracking pressure refers to the inlet pressure level at which the first sign of flow is present. It can also be described as a measure of the pressure differential between the inlet and outlet ports of the valve when flow is initially detected. So, the answer is yes. If there is a loss of pressure on the downstream side of the check valve that results in a differential pressure that exceeds the cracking pressure, the valve will open and begin to flow.
For more than 75 years, DFT® Inc. has helped customers find and install the right check valves for their unique applications. To learn more about our valves, and how we can assist you, contact us directly.
Comments are closed